目次
鍛造の温度
鍛造の温度鍛造は溶解温度近辺から室温までの広い温度範囲で行われます。
室温未満の温度でも鍛造は可能ですが、今のところメリットが見いだされていないので行われていません。
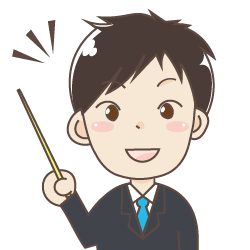
鍛造温度は対象とする製品の大きさ、材料の種類、材料の変形抵抗・変形能、鍛造設備の制約、製造数量の多少、競合するプロセスとのコスト対比など種々の因子を考慮して決めなければなりません。
ここでは鍛造温度決定の考え方について説明します。
鍛造における温度の選択
温度域による鍛造法の分類
熱間鍛造では材料を再結晶温度以上に加熱することで柔らかく、大変形させても破壊しにくい状態にして圧縮応力状態下で変形を付与するとともに材質的改善を行います。
しかし鍛造品表面の酸化や寸法精度の低下、工具表面のダレや摩耗、過熱作業に伴う作業環境の悪化、さらにはエネルギーコストの問題などが生じます。
変形が温度に敏感な材料では金型の温度を制御することも必要になることがあります。
一方、室温で行う冷間鍛造では高強度で高寸法精度・高表面品質の部材が高生産性で得られますが、工具に大きな負荷が加わることや変形に伴い材料がもろくなって鍛造中に割れが生じたり、残留応力による寸法変化を生じたりするなどの問題が起こります。
温間鍛造は再結晶温度以下に加熱する鍛造方法であり、材料の変形抵抗を低下させ加工熱処理を行う上でも有用です。上述のような考えで鍛造法を成形温度域で整理すると半凝固鍛造・熱間鍛造・温間鍛造・冷間鍛造に分けられます。
それぞれの特徴と温度域を選定する狙い目と材種について
半凝固鍛造
狙い目 |
変形抵抗が極端に小さく、複雑な形状に成形できます。 |
特徴 |
成形による組織の微細化や材質改善、鍛造で成形と接合による複合化、加熱・冷却の厳しい温度管理が必要、金型の熱負荷が大きいなどがあります。 |
材種や製品例 |
アルミニウム合金・マグネシウム合金・鋳鉄などがあります。 |
熱間鍛造
狙い目 |
加熱で柔らかく(低変形抵抗)、変形しやすい(高変形能)状態で鍛造、室温で硬くもろい材料、特大サイズ、複雑形状品に最適。鍛造組織や偏析の微細化、再結晶による変形能の増大などが見込まれます。 |
特徴 |
材料表面の酸化、工具のダレ・摩耗により型寿命が短い、寸法精度が温間や冷間より悪い、材料によっては適切な潤滑剤が必要などがあります。 |
材種や製品例 |
鉄鋼(クランクシャフト、発電機用軸類、自動車や建機用部品など)アルミニウム合金(航空機部材、電機用部品など)チタン合金・超合金(エンジンディスク、タービンブレードなど)銅合金 |
温間鍛造
狙い目 |
熱間と冷間の得失を兼備した方法で、変形抵抗低減、変形能増大による高精度の鍛造ができます。 |
特徴 |
加工熱処理(オースフォーミングなど)による鍛造品の強靭化が可能になり、熱間より酸化スケールが減少します。 |
材種や作品例 |
鉄鋼(自動車部品、ボルト、ナット、一般産業機械部品、軸受部品など小物製品)アルミニウム合金、純銅 |
冷間鍛造
狙い目 |
変形抵抗が大きく加工硬化を伴いますが、寸法精度・表面状態が良好で鍛造のままでも使用可能です。 |
特徴 |
材質上変形させやすい成分のものが必要です。 工具に大きな負荷が加わり、適切な潤滑剤が必要になります。 |
材種や作品例 |
温間鍛造と同じです。 |
原料から鍛造に至る工程と温度とのかかわり
鍛造部材の製造においては、鍛造前素材を作る1工程目とそれを鍛造により最終製品もしくはそれに近い形状・品質にまで仕上げる2工程目に分けられます。
1工程目においては溶湯から鋳塊にしたのち熱間自由鍛造・押出し・圧延などの方法により鋳造組織を壊したり、鋳塊内部の空隙を消滅させたりして材質改善を図る方法と小物鍛造前素材用に冷間で引抜きや圧延を行う方法とがあります。
鉄鋼・アルミニウム合金・銅合金・チタン合金などはこの方法で鍛造前素材が準備されます。
1工程目には溶湯を噴霧して金属粉末にしたのち熱間圧密(HIP)あるいは冷間圧密(粉末鍛造、CIP)により鍛造前素材を作る方法もあります。
前者(HIP)にはNi基超合金などのように鋳造のままでは割れやすく、熱間変形抵抗が極端に高くなります。
変形させやすくするために微細結晶組織にすることが必要な材料に属します。
後者(CIP)には合金鋼粉末の焼結鍛造(コネクティングロッドなど)や粉末焼結品が属します。
また、溶湯を半凝固状態で噴霧堆積(オスプレイ法)させることによりビレット(素材)を作成し、それを鍛造や押出しにより鍛造前素材とすることもあります。
2工程目における鍛造は鍛造方式により自由鍛造と型鍛造とに分かれ、型鍛造には半密閉型と密閉型とがあります。
熱間自由鍛造は主に大型製品の少量生産に用いられ、半密閉鍛造はバリを出しながら金型の角部にも材料を充満させて形状を整えます。
この方法は主に熱間で行われ、バリが材料歩留まりを悪くします。
バリをなくし鍛造品精度を高めるために熱間・温間・冷間のいずれにおいても密閉型鍛造が採用されます。
鍛造温度決定の道筋
前述の2工程目においては、鍛造前素材をいかにして「低コストで精度良く最終形状・品質」に近づけるかを念頭において、熱間・温間・冷間あるいはそれらの組み合わせによる鍛造方法が選択されます。
選択に当たっては「鍛造の限界」を生じさせる因子は何かをまず考え、次に「品質を満たしながらコスト低減が可能な手段」は何かに創意工夫をすることになります。
鍛造の限界にかかわる因子は材種と製品形状が与えられた場合、設備があるか?」と「鍛造しても割れないか?」の2つを考えます。
鍛造設備・変形能の観点から鍛造可能となれば、次に品質・コストの観点から製品の材質・金型構造・生産量などを考慮に入れて鍛造方式、加熱方法や鍛造温度の適正化、潤滑剤の選定などいわゆる低コスト鍛造できる条件設定が行われます。
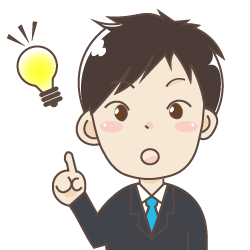
鍛造中の温度変化
材料に塑性変形を与えると変形のエネルギーが熱に変化し、鍛造品や金型の温度上昇をもたらします。
単位体積あたりに仕事wがなされたとき、変形が断熱的に行われるとき変形後の温度Tpは次式のようになります。
式1 | Tp=Tp+βw/JρC |
ここで、Tbは素材の温度、Jは仕事の熱等量、ρおよびCはそれぞれ材料の密度および比熱を示します。
式1から分かるように材料の密度ρ、比熱Cが小さいアルミニウム合金やチタン合金では鍛造品の温度上昇が大きいです。
熱間鍛造や温間鍛造では金型温度より鍛造品温度の方が高いので、接触面では鍛造品から金型に熱が奪われます。
接触面での単位時間の熱移動量(熱流束)は素材温度Tmと金型温度Tdとの差に比例し、熱コンダクタンスをKcとすると次式で表されます。
式2 | W=Kc(Tm-Td) |
素材と金型との温度差が大きく、接触時間が長くなるほど鍛造品の温度が低下します。
材料が持つ熱量は表面積、つまり、寸法の2乗に比例します。
このため、製品寸法が大きくなるに従い温度が冷却しにくくなるのに対し、製品が小さくなるほど冷却が激しく熱間鍛造が難しくなります。
また、加工時間が長くなると奪われる熱量が大きくなるので、加工速度は素材温度の低下を考慮して決定されます。
鉄鋼系材料では変形抵抗を速くしても変形抵抗が若干増加する程度なので、金型/鍛造品温度比を低く設定し、鍛造速度を速くして鍛造品の温度低下を抑えようとします。
変形抵抗や変化能が温度に敏感なチタン合金の鍛造では750℃~900℃の範囲でハンマーによる高速鍛造を採用しないと十分な変形が与えられません。
アルミニウム合金の熱間精密鍛造では金型温度が350℃~400℃に設定されるので、金型/鍛造材温度比は0.8程度で油圧プレスやクランクプレスを用いて中速度(5~15mm/s程度)で鍛造されます。
アルミニウム合金のように密度・比熱が共に小さい材料では式1のように変形に伴う発熱が大きくなり、結晶粒の粗大化が生じるなど機械的性質が好ましくない場合が発生します。
金型温度は鍛造品温度より50℃~100℃程度低いので鍛造中に金型との接触により鍛造品の温度低下が生じます。
変形と摩擦による発熱と金型との熱授受を考慮した熱連成変形シミュレーションでアルミニウム合金鍛造品および金型の温度を予測した場合、厚肉部では金型との接触で材料温度は初期温度よりも低下していますが、薄肉部では変形量が大きく材料温度は初期温度より40℃~50℃高くなります。
実際の鍛造では素材加熱温度や鍛造速度の設定に注意し、品質の劣化を防止する必要があります。
熱間の変形抵抗が極端に高い耐熱合金やチタン合金の精密鍛造では超塑性特性(結晶粒を微細にして低ひずみ速度下で変形能が大きく、変形抵抗が小さくなる状態)を付与した材料を金型温度と素材温度をほぼ同一にして低速で鍛造することでニアネットシェイプに仕上げます。
材種別の鍛造事例
鉄系材料
大型部材の自由鍛造
ロータ・クランクシャフト・船舶用軸物などは熱間自由鍛造あるいは部分的な熱間型鍛造などで製造されます。
数百tの大型インゴットの中央内部には鋳塊の大きさや形状に依存して空隙が存在するので、1100℃~1200℃の高温で1万t(100MN)クラスのプレスを用いて圧縮し、内部に高い静水圧応力状態を作り出して大変形させることによって空隙を圧着させるとともに鋳造組織を破壊します。
いわゆる鍛錬効果を与えて材質を改善します。
これを効果的に行うために材料表面温度を中心部よりも低くして、中心部に変形が及びやすいように工夫したり、金敷きの大きさや形状を適性にして静水圧成分が高まるように工夫したりします。
大型品の自由鍛造では電気炉やガス炉による素材加熱に数時間を要することもあるので、加熱エネルギーを節減するため可能な限り低めの温度にすることが望まれますが、一方で鍛造時間が30~60minにも及ぶので、その間の温度低下により鍛造重が増大し、プレス力量が不足することもあります。
これは再加熱の繰り返しによるコストアップ、結晶粒の粗大化による品質低下を招くことになります。
このため鍛造中の材料の保温は重要で、断熱材を巻き付けたり、発泡系の断熱材を加熱された材料に直接吹き付けたりする方法などが現場では採用されています。
鉄鋼の精密鍛造
炭素鋼・ステンレス鋼・軸受鋼・工具鋼などの鍛造ではネットシェイプ化が求められ、熱間・温間・冷間鍛造が使い分けされます。
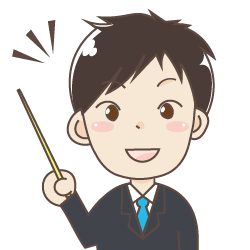
温間鍛造では冷間に比べ変形脳が上昇し、変形抵抗が低下する特徴を持ちます。
また加熱処理を行うことも可能ですが、温度選択に当たっては炭素鋼に見られる青熱脆性や赤熱脆性温度域を避けること、ステンレス鋼では変形抵抗の低下率が急増する温度域(例えばステンレス鋼では200℃~400℃)が存在することなどに注意する必要があります。
銅合金系材料
青銅など銅合金の鋳造品は古代から重宝されてきましたが、鋳造組織を壊し強靭さを加えるために鍛造や押出しが行われます。
純銅の成形には冷間・温間鍛造が用いられますが、変形能に限界がある銅合金では熱間鍛造が主流です。
銅合金は350℃~450℃に脆性温度域が存在しますので、600℃~900℃の範囲で鍛造されます。
黄銅の熱間における組織はα相・(α+β)相・β相であり、α相は他の2相よりも延性が低く、変形抵抗が高いです。
また、β相を長時間加熱すると結晶粒が成長し変形時に粒界割れを起こしてしまうので、β相が多い(α+β)相領域になるように鍛造温度を選択します。
加熱時の温度と保持時間には注意が必要で、誘導炉を用いた短時間加熱が推奨されます。
アルミニウム系材料
アルミニウム系材料でできた小サイズの部材は熱間押出し材を切断・機械加工する方法や冷間鍛造による方法で製造されます。
一方、大型のアルミニウム合金鍛造品にはは400℃~470℃の熱間で鍛造され、高精度の寸法・形状ではメタルフローが制御された高品質のものが航空機や自動車用に供給されます。
アルミニウム合金の熱間精密鍛造では電気炉やガス炉で加熱された素材を、それより50℃程度低めに加熱された金型を用いて、精度の高い大容量のプレスによって最終製品形状に仕上げます。
そのため抜け勾配を30´~1°程度小さくし、コーナーRも極力小さくするとともに、型分割位置をグレンフローの要求に合致するように配慮することが必要です。
鍛造品の用途上品質確保の要求が強く、鍛造温度は±20℃以内で管理され、強度や耐食性を支配するグレンフローの制御、局所的な結晶粒成長の防止、焼付きの防止などが重視されます。
この観点では鍛造用素材の形状、型設計、潤滑剤、鍛造速度制御が重視され変形シミュレーションや温度変化予測が利用されます。
チタン合金およびニッケル基超合金などの耐熱材料
一般的に耐熱材料と呼ばれる材料は高価で、切削性が悪いので熱間精密鍛造のニーズが高いです。
しかし、熱間での変形抵抗が高く、鍛造可能温度域が狭いので材料が超塑性挙動を示す条件下で熱間精密鍛造を行います。
鍛造素材に関しては変形抵抗を低くするために鍛造前素材の結晶粒を数μm以下に微細化して、超塑性挙動を示すように調整します。
また、成形に際しては超塑性挙動を示すときのひずみ速度は低ひずみ速度でなので低速度鍛造であり鍛造荷重は低いものの、鍛造可能温度域が狭いので、金型温度は鍛造素材とほぼ同温に保って鍛造中の温度低下を防ぐことが必須になります。
Ni基超合金部材の製造工程は、原料粉末を固化して鍛造素材を作製する場合に微細結晶粒になるように粉末製造段階で細粉したり、熱間押出しでひずみを与えたりする方法が採用されます。
その後超塑性鍛造により所定の形状に鍛造されます。