目次
超硬合金の基本特性とメリット
超硬合金は、その高い硬度と優れた耐摩耗性から、さまざまな産業で重要な役割を果たしています。これは、タングステンカーバイドなどの硬質成分が結合し、非常に強固な素材が形成されるためです。例えば、切削工具や金型に使用されることで、高精度で長寿命の製品を生み出すことが可能となります。そのため、過酷な条件下でも安定した性能を発揮する超硬合金は、信頼性が高く、多くの業界で重宝されています。
高硬度・耐摩耗性に優れる理由
超硬合金が高硬度かつ耐摩耗性に優れている理由は、主成分であるタングステンカーバイドの特性によるものです。この成分は非常に硬く、摩耗しにくい性質を持っているため、長期間の使用でもその性能を維持します。具体的には、採掘や金属加工で使用される工具に採用されており、耐久性が求められる場面で活躍しています。このように、長持ちすることから、コストパフォーマンスも優れています。
超硬合金が使用される産業分野
超硬合金は、自動車や航空宇宙産業、工具製造などの分野で幅広く使用されています。これらの産業では、耐久性と精度が求められるため、超硬合金の優れた特性が最適です。例えば、自動車部品の製造では、複雑な形状を高精度で加工する必要があり、超硬合金の使用が不可欠です。また、航空機のエンジン部品にも使用され、信頼性の高い製品を提供しています。
超硬合金の加工における主な課題
超硬合金の加工には高度な技術が求められます。硬度が非常に高いため、通常の加工方法では工具が摩耗しやすく、加工コストが増加します。例えば、精密な切削加工を行う際には、高価な専用工具や機器が必要です。このため、加工技術者は適切な工具選定や最適な加工条件を見極める必要があります。効率的な加工を実現するためには、技術者のスキルも重要です。
高硬度ゆえの加工の難しさ
超硬合金の加工は、その硬度の高さゆえに困難です。加工中に工具が摩耗するだけでなく、温度の変化や衝撃によって割れやすい素材でもあります。例えば、放電加工を使用しても微細なクラックが発生することがあり、仕上げ精度に影響を与えることがあります。このように、加工時のリスクを軽減するためには、加工速度や工具の選定が重要です。
割れやすさと加工精度の両立
超硬合金は、加工中に割れやすい特性を持つため、高い精度での加工が求められます。これを実現するためには、工具の選定や加工方法の最適化が不可欠です。例えば、低速での切削や放電加工を組み合わせることで、素材の割れを防ぎながら精密な仕上げが可能になります。このように、慎重な操作と高い技術力が、加工の成功につながります。
超硬合金の主要な加工方法
超硬合金の加工には、複数の方法が存在します。それぞれの加工方法は、目的や素材の特性に応じて選ばれます。切削加工、研削加工、放電加工、ラップ加工などの方法が一般的で、それぞれの方法がもたらす利点や制約を理解することが、加工の成功に繋がります。こうした加工方法を適切に組み合わせることで、製品の品質と効率を最大化することが可能です。
切削加工の特徴と適用範囲
切削加工は、超硬合金の外形や形状を整えるために使用されます。超硬合金の高硬度により、切削工具の耐久性が問われますが、精密な切削が可能です。例えば、精密な金型や工具の製造において、微細な形状を実現するために使用されます。切削加工は、高速かつ正確に形状を仕上げる方法として広く採用されています。
研削加工での仕上げ精度の向上
研削加工は、超硬合金の表面を平滑に仕上げるための方法です。高硬度の超硬合金でも、適切な砥石を使用することで微細な表面処理が可能です。特に、工具や部品の仕上げ精度が求められる際に、この方法が効果的です。例えば、金型製作において、極めて高い精度を求められる部品の仕上げに使用されます。
放電加工による精密加工の利点
放電加工は、超硬合金の硬さに関わらず、複雑な形状や微細な加工が可能な方法です。非接触で加工が行えるため、素材への熱や圧力の影響を最小限に抑えながら、非常に高い精度を実現します。例えば、深穴加工や微細なパターンの形成が求められる場合に放電加工が採用され、精密な製品が製造されます。
ラップ加工での超精密仕上げ
ラップ加工は、超硬合金の表面を極めて滑らかに仕上げるための加工方法です。微細な研磨剤を用い、加工表面に対して均等な圧力をかけて仕上げます。特に、高精度が求められる光学部品や機械部品において、仕上げ精度を向上させるために使用されます。このように、ラップ加工によって製品の表面品質が大きく向上します。
レーザー加工の精密性と適用範囲
レーザー加工は、超硬合金の切断や彫刻に使用される方法で、その高い精密性が特徴です。熱による加工でありながら、微細な形状の形成や複雑な模様の彫刻が可能です。例えば、工具の彫刻や部品の微細加工において、その精度の高さが活かされています。レーザー加工は、非接触で行えるため、超硬合金の硬さに影響されずに加工が可能です。
旋盤加工による効率的な加工方法
旋盤加工は、回転体の加工に最適な方法で、効率的に超硬合金の外形を整える手段です。旋盤による加工は、特に円筒形の部品や工具の製造において、精密かつスピーディに行われます。例えば、軸やピンなどの部品製作において、超硬合金の特性を活かしつつ、迅速に加工できる方法として重宝されています。
超硬合金加工における成功のポイント
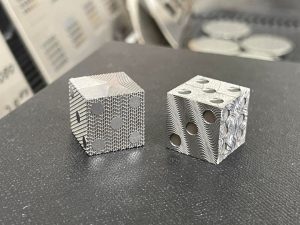
超硬合金のサイコロです
超硬合金の加工を成功させるためには、いくつかの重要なポイントがあります。特に、加工条件の設定や機器の選定、技術者のスキルが大きく影響します。これらの要素を適切に管理することで、製品の品質を高め、コストを抑えつつ効率的な加工が可能となります。成功するためのポイントをしっかりと把握することが、安定した品質と効率的な生産につながります。
適切な加工条件の設定
超硬合金の加工において、最適な加工条件を設定することが成功の鍵となります。例えば、切削速度や工具の角度、冷却方法などを適切に設定することで、工具の摩耗を抑えつつ精度の高い加工が可能となります。特に放電加工や研削加工では、微細な条件設定が仕上げに大きく影響します。こうした調整が、加工効率と品質を大幅に向上させます。
加工機器の選定とその重要性
超硬合金の加工には、専用の高精度な機器が必要です。例えば、高硬度の素材を効率よく加工するためには、強力な切削機や放電加工機が不可欠です。また、適切な機器の選定は、製品の仕上がりや加工時間に直接的な影響を与えます。最新の技術を取り入れた機器を選定することで、品質向上とコスト削減の両方が実現できます。
加工技術者のスキルが成功のカギ
超硬合金の加工には、経験豊富な技術者のスキルが不可欠です。高精度な加工を行うためには、加工機器の操作や条件設定に熟練した技術者が必要です。例えば、放電加工や研削加工では、微細な調整が製品の品質を左右します。技術者の経験と知識があれば、より複雑で精密な加工にも対応でき、結果として高品質な製品が生み出されます。
超硬合金加工の事例紹介
実際の超硬合金加工の事例を紹介することで、その技術力と精度を示すことができます。高精度な金型部品や特殊形状の工具製作など、具体的な事例を通して、超硬合金加工の応用範囲を理解することができます。これにより、依頼主は加工の可能性や自社のニーズに合った技術を確認でき、信頼性の高い加工依頼を行うことができます。
高精度な金型部品の製作事例
超硬合金を使用した金型部品の製作では、微細な精度が求められることが多くあります。例えば、複雑な形状の金型製作において、放電加工や研削加工が用いられ、極めて高い精度で部品が作られます。このような事例では、超硬合金の特性を最大限に活かし、耐久性と精度を両立させた製品が提供されています。
特殊形状の超硬工具製作の成功例
特殊形状の超硬工具の製作では、高度な加工技術が必要です。例えば、円筒形や複雑な刃形状を持つ工具の製作では、放電加工や切削加工を駆使して、正確かつ効率的な製造が行われます。この成功例では、超硬合金の高硬度を活かし、長寿命かつ高精度な工具が製作され、各種産業で使用されています。
超硬合金加工の依頼時に知っておくべきポイント
超硬合金加工を依頼する際には、いくつかの重要なポイントを理解しておく必要があります。依頼先の選定基準や、コストと納期の見積もり方法などを知ることで、効率的かつスムーズな依頼が可能となります。これにより、製品の品質を保ちながら、適切な予算とスケジュールで加工を進めることができるため、依頼者にとっても安心です。
依頼先の選定基準
超硬合金加工を依頼する際の選定基準として、技術力、実績、設備の充実度が重要です。例えば、最新の加工設備を保有し、過去に多くの高精度な製品を手掛けた企業は、信頼性が高いです。こうした選定基準をもとに、加工依頼を行うことで、品質の高い製品が期待できます。また、事前に企業の事例や評判を調査することも有効です。
コストと納期の見積もり方法
加工依頼時には、コストと納期の見積もりが非常に重要です。超硬合金の加工は高精度を求められるため、費用が高くなる場合がありますが、適切な見積もりを取ることで予算管理がしやすくなります。具体的には、加工内容や素材の特性を考慮し、納期を含めた詳細な見積もりを複数の業者に依頼することが推奨されます。


代表取締役社長 中村稔
詳細プロフィールは⇒こちら