先進技術が日々進化を遂げる中で、ステンレス加工技術もまた、その波に乗り新たな地平を切り開いています。微細な穴あけ加工から複雑な凹凸加工に至るまで、精密な技術の進歩は、ステンレス製品の機能性と効果を高め、私たちの身の周りのものをより便利にしてくれています。本記事では、ステンレス(SUS)加工技術の最前線に立つ革新的な技術動向と、その応用事例を深掘りして現在の技術と未来の可能性について解説します。
目次
微細な穴あけ加工:ステンレスの精密性を極める
微細穴あけ加工技術は、ステンレス製品の精密性を大幅に向上させる革新的な方法です。この技術により、極めて小さな穴を高精度で加工することが可能になり、医療機器や精密機械部品など、高度な精密さが求められる製品の製造に貢献しています。最新の技術動向には、レーザー加工や電気化学加工などがあり、これらは製品の品質向上だけでなく、生産効率の改善にも寄与しています。応用事例としては、微細な医療用カテーテルの製造などが挙げられます。ニッシンパーテクチュアルでは数μ~数十μでの穴あけ加工が可能です!

ステンレスの穴あけは幅広い分野でニーズがあります。医療、自動車、精密部品など最先端のテクノロジーになればなるほどより小さく深く精度が求められます。
ステンレス(SUS)における精密な溝(リブレット形状)加工の進化
ステンレス製品の微細溝加工技術は日々進化を遂げており、製品の機能性向上に大きく寄与しています。この技術の進歩により、ステンレス表面に微細な溝を精密に加工することが可能となり、摩擦低減や流体の制御といった機能を製品に付加できるようになりました。特に、自動車部品や電子機器の小型化が進む中で、この技術の重要性は高まっています。進化する溝加工技術は、より複雑で精密なデザインの実現を可能にし、ステンレス製品の新たな可能性を切り開いています。

ステンレスの溝加工は空気や液体の抵抗を高めたり低めたりします。こちらの技術もいろいろな分野、製品に使われています。最先端なテクノロジーなので研究開発の議題にもなってます!
美と機能を兼ね備えたステンレスの極小ディンプル(ブラスト)加工
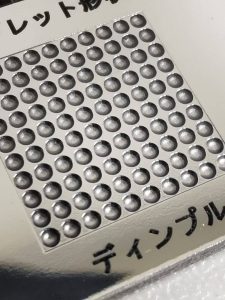
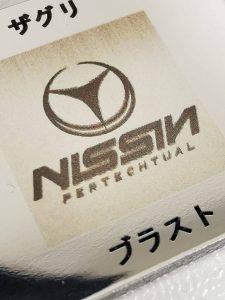
ステンレス製品における極小なディンプル加工は、外観の美しさと機能性の向上の両方を実現します。この加工により、製品表面に小さな凹凸を作り出すことができ、光の反射や質感を変化させることで、美観を高めることが可能です。また、ディンプルの形状や配置を工夫することで、空気抵抗の低減や熱伝導性の向上といった機能的なメリットも得られます。例えば、スポーツ用品や自動車のエアロパーツに応用され、性能向上に寄与しています。

抵抗の低減や熱伝導率の機能性を高めたり、光の反射を抑制するためにブラスト、密着性を低減するための数μ程のディンプル加工など様々な形状があります。ディンプルも奥が深い!
ステンレスの凹凸加工で微細なデザインが開く未来
ステンレスの凹凸加工技術は、製品の美観と機能性を高めるための重要な手法です。この技術を利用することで、表面に微細な凹凸パターンを作り出し、視覚的な魅力を高めると同時に、触感を改善することができます。また、凹凸の形状によっては、製品の機能性にも影響を与えることがあり、例えば、滑りにくさの向上や、汚れが付きにくい表面の実現が可能です。この技術の進展により、ステンレス製品はより魅力的で機能的なものへと進化しています。
四角錐と逆四角錐の加工
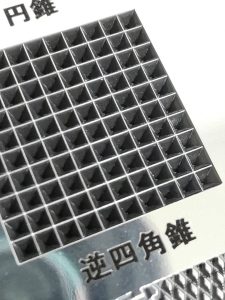
四角錐と逆四角錐の加工は、高度な切削技術と精密な制御が求められます。四角錐の加工では、平面と斜面の正確な削り出しが重要で、均一な角度と滑らかな表面仕上げが求められます。逆四角錐の場合は、内部から外部に向かって広がる形状を高精度に加工するために、特殊なマシンと加工方法が必要です。これらの形状は、航空機部品や精密機器の製造において重要な役割を果たします。
円錐と逆円錐の加工
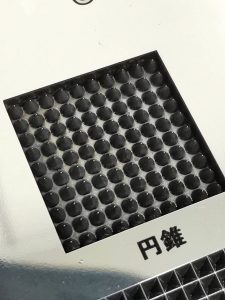
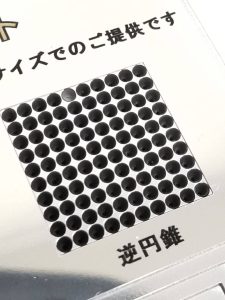
円錐および逆円錐の加工は、高度な精密加工技術が必要です。レーザー加工は、この形状を微細かつ高精度に実現するために非常に有効です。レーザー加工では、非接触で材料を除去するため、工具摩耗の心配がなく、複雑な形状を高精度で仕上げることができます。特に逆円錐の加工では、内部から外部に向かって広がる形状を高精度に加工でき、航空宇宙や医療機器などの分野で重要な役割を果たします。

凹凸形状といってもピラミッド状の四角錐、円筒、円柱、複雑形状の立体モデルなど数μ~数十μ単位での形状が求められます。
ステンレスのシボ加工
シボ加工とは、ステンレスの表面に微細な凹凸や模様を施す加工法です。この加工により、製品の美観や機能性が向上します。シボ加工は、デザイン性を高めるだけでなく、指紋や汚れが目立ちにくくなる効果もあります。化学エッチングや機械的な手法を用いて、均一で高精度な模様を実現できます。ステンレス製品の外観品質を向上させるために、自動車や建築、家電製品などで広く利用されています。
ザグリ加工
大きな凹みを加工する方法です。この加工により表面より下に平滑な表面を保つことができます。特に機械部品の組み立てにおいて、部品同士の密着度を高め、強度や安定性を向上させます。主にフライス盤や専用のザグリカッターを使用し、高精度で均一な仕上がりを実現します。
ステンレスの微細加工に使われる手法
切削技術によるステンレスの精密加工
最先端の切削技術は、ステンレスの微細加工分野に革命をもたらしています。この技術により、非常に小さな部品や複雑な形状の加工が高精度で可能になり、製品の品質と性能の向上が実現しています。特に、医療機器や精密機械部品など、高度な精密さが求められる分野での応用が進んでいます。切削技術の進化により、加工の効率化やコスト削減も期待されており、今後のさらなる技術革新が注目されています。
レーザー技術によるステンレス微細加工の可能性
レーザー加工技術によるステンレスの微細加工は、その精密さと効率性から多くの分野で注目されています。この技術は、非接触で加工が行えるため、材料の損傷が少なく、非常に細かい部分まで精密に加工することが可能です。レーザー加工は、医療機器の製造や電子機器の部品加工など、幅広い応用が見込まれており、特に複雑な形状や極細の加工が求められる場合にその真価を発揮します。この技術の進化により、新しい製品開発や既存製品の品質向上が期待されています。
放電加工によるステンレス微細加工の革新
放電加工技術は、ステンレスの微細加工において高い精密さと効率性を実現しています。この技術は、放電現象を利用して材料を加工する方法で、特に硬質材料や複雑な形状の加工に適しています。放電加工により、スムーズな表面仕上げや複雑な形状の精密加工が可能となり、航空宇宙や医療機器などの分野での応用が進んでいます。技術の進歩により、加工時間の短縮やコスト削減も実現しており、今後の更なる応用拡大が期待されます。

ニッシンパーテクチュアルでは切削、レーザー、放電など様々な加工方法から最善、最良のものにお応えできるように日々精進しております。
ステンレス加工技術の進化は、私たちの日常生活や産業界に革命をもたらすポテンシャルを秘めています。微細加工技術が進化することで、より精密で高機能な製品の開発が可能となり、未来の医療機器から日用品に至るまで、幅広い分野でその影響を見ることができるでしょう。今回ご紹介した技術動向と応用事例は、この分野の可能性のほんの一部に過ぎません。技術のさらなる進化とともに、ステンレス製品の新たな価値が未来にどのように展開していくのか、大いに期待されます。今後も、この興味深い進化の旅を見守っていきましょう。


代表取締役社長 中村稔
{
“@context”: “https://schema.org”,
“@type”: “ImageObject”,
“contentUrl”: “https://pertechtual.co.jp/wp-content/uploads/2024/04/1717460476609.jpg”,
“name”: “ステンレス(SUS304)微細加工”,
“description”: “ステンレスへディンプル、リブレット、ブラストなどの微細な加工を施したものです。”,
“author”: {
“@type”: “Organization”,
“name”: “ニッシン・パーテクチュアル株式会社”
},
“datePublished”: “2024-06-04T09:27:00+09:00”,
“width”: “1080”,
“height”: “1440”
}